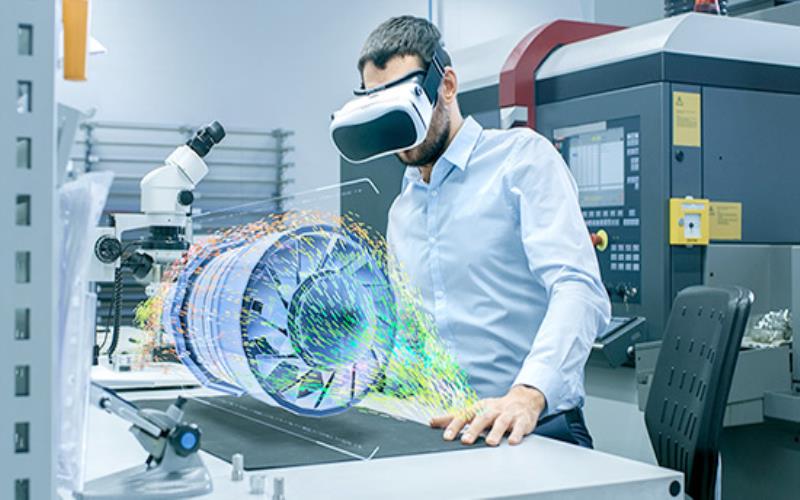
As someone who has worked in the field of materials science for many years, I’ve always been fascinated by the incredible potential of thin films.
These ultra-thin layers of material, ranging from a few atoms to several micrometers in thickness, have revolutionized countless industries – from semiconductors and solar cells to optical coatings and biomedical implants.
At the heart of this technological revolution are the various thin film deposition techniques that allow us to precisely control the composition, structure, and properties of these films.
In this article, I’ll provide an overview of the most common deposition methods and explore some of the exciting applications they enable.
Physical Vapor Deposition (PVD)
One of the two main categories of thin film deposition is physical vapor deposition or PVD. As the name suggests, PVD involves physically vaporizing a material and allowing it to condense on a substrate to form a thin film.
The two most widely used PVD techniques are evaporation and sputtering.
Evaporation
In evaporation, the source material is heated in a high vacuum until it vaporizes. The vapor then travels through the vacuum chamber and condenses on the cooler substrate, gradually building up a thin film atom by atom.
This technique is often used to deposit metals like aluminum for electronic contacts or optical coatings.One of the key advantages of evaporation is its simplicity and low cost.
However, it can be difficult to control the stoichiometry of alloys or compounds, and the films tend to be less dense and adhesive compared to other methods410.
Sputtering
Sputtering, on the other hand, involves bombarding a target material with energetic ions, typically argon plasma, to eject atoms which then deposit on the substrate. By applying a magnetic field, the plasma can be confined near the target in a configuration known as magnetron sputtering, greatly increasing the deposition rate and efficiency.
I’ve found sputtering to be an incredibly versatile technique, allowing the deposition of a wide range of materials from pure elements to alloys and compounds. The films are also generally denser, more uniform, and have better adhesion than evaporated films.
Common applications include hard coatings on tools, low-emissivity window films, and the recording layers on CDs and DVDs.
Chemical Vapor Deposition (CVD)
The other major category of thin film deposition is chemical vapor deposition or CVD. Rather than physical vaporization, CVD relies on chemical reactions between volatile precursors, usually in the gas phase, to deposit a film on the heated substrate surface.
Thermal CVD
The most basic form of CVD is thermal CVD, where the substrate is simply heated in a chamber containing the precursor gasses. At sufficiently high temperatures, the gasses react and deposit a solid film on the surface.
Thermal CVD is widely used in the semiconductor industry to deposit dielectric films like silicon dioxide and silicon nitride.
Plasma-Enhanced CVD (PECVD)
To lower the deposition temperature and improve film quality, plasma-enhanced CVD or PECVD is often used. By applying a plasma, typically with radio frequency (RF) power, the precursor gasses become ionized and more reactive, allowing deposition at much lower substrate temperatures.
This is critical for applications like solar cells and flat panel displays, where the substrate may be temperature-sensitive.
In my experience, one of the key advantages of CVD techniques is the ability to deposit highly conformal films, even on complex 3D structures. This has become increasingly important as device dimensions continue to shrink in the semiconductor industry.
Atomic Layer Deposition (ALD)
For the ultimate in thickness control and conformality, atomic layer deposition or ALD has emerged as the technique of choice. ALD is based on sequential, self-limiting surface reactions between alternating pulses of precursor gasses.
By exposing the substrate to one precursor at a time, waiting for it to saturate the surface, and then purging the chamber before introducing the second precursor, films can be grown with atomic level precision.
While ALD is typically slower than other deposition methods, its unique capabilities have made it indispensable for many cutting-edge applications. These range from high-k gate dielectrics and diffusion barriers in advanced logic devices to passivation layers for quantum dots and nanostructured battery electrodes.
Applications of Thin Films
The diverse properties and capabilities of thin films have enabled a staggering array of applications across virtually every industry and aspect of modern life. Here are just a few examples that I find particularly exciting:
Solar Cells
Thin film photovoltaics, based on materials like cadmium telluride (CdTe), copper indium gallium selenide (CIGS), and perovskites, offer the potential for low-cost, high-efficiency solar energy conversion.
By using techniques like sputtering, PECVD, and thermal evaporation, these semiconductor films can be deposited on large-area, flexible substrates, opening up new possibilities for building-integrated and portable power generation.
Solid-State Lighting
The development of high-brightness LEDs and organic LEDs (OLEDs) has revolutionized the lighting and display industries. Thin films play a crucial role here, from the quantum well structures that generate light in inorganic LEDs to the emissive and charge transport layers in OLEDs.
By carefully controlling the composition and thickness of these films with techniques like MOCVD and thermal evaporation, the color, efficiency, and lifetime of these devices can be optimized.
Biomedical Coatings
Thin film coatings have also found widespread use in the biomedical field, particularly for improving the biocompatibility and functionality of implantable devices.
For example, titanium dental implants are often coated with thin hydroxyapatite films to promote osseointegration, while cardiovascular stents may be coated with drug-eluting polymers to prevent restenosis.
Techniques like magnetron sputtering and PECVD are well-suited for depositing these bioactive coatings.
Conclusion
From the atomic scale to the global stage, thin film deposition techniques have truly transformed our world. As we continue to push the boundaries of materials science and nanotechnology, I believe these methods will only become more important and enabling.
Whether it’s developing more efficient solar cells, brighter and longer-lasting solid-state lighting, or smarter and safer biomedical devices, the future of thin films is bright indeed.
As someone who has dedicated their career to this field, I can’t wait to see what groundbreaking innovations the next generation of materials scientists and engineers will achieve with these remarkable tools at their disposal.
Source: Explore